Fuel
Injectors
by:Titan
There are 6 basic types of metering devices used in fuel injectors
today but I will only cover the 3 that I feel will have the most
impact. The first is the pintle type made by Bosh/Nippon Denso.
This single pintle discharge injector tends to increase atomization
and pattern width at higher pressures. Next, is the disk type fuel
injector manufactured exclusively by Lucas. This injector possesses
stainless steal internals and a unique metering disk that is years
ahead of the 40 year old pintle type injector. The Lucas injector
is the best at maintaining its spray pattern cycle to cycle, under
varying pulse widths and fuel pressures. Lastly, there is the diffuser/pintle
type injector found on Toyota and various other makes and models.
Diffuser/pintle type injectors do not change atomization quality
at higher fuel pressures like the Bosh/Nippon Denso type injectors.
Diffuser/pintle injectors are not high atomizers, they are used
to target fuel toward the valve stem reducing intake wall wetting
or "puddling" of the fuel. This targeted approach is accomplished
by the impact of the fuel on the diffuser surface, which concentrates
the fuel at the center of the cone producing a tighter pattern.
The distance from the injector to the valve and the cross sectional
area of the intake must be considered when incorporating this injector.
Injector types
Peak and Hold injectors, also called low impedance, are initially
fired at 4-6 Amps, through a ballast resister, and then fall back
to 1-2 Amps for the rest of the injection event. This injector is
often used on high fuel pressure systems (75-100psi+) where the
increased initial amperage overcomes the high hydrostatic pressures
of the fuel pressure. Peak and Hold injectors These injectors tend
to respond faster than Saturated injectors
Capabilities
The minimum pulse width cycle time for most pintle type fuel injectors
(Bosh/Nippon-Denso) is 2.0Ms for the Peak and Hold and 2.5Ms for
the Saturated injectors. Alternatively, disc type injectors (Lucas)
will cycle as low as 1.0Ms for Peak and Hold and 2.0Ms for Saturated.
The difference in pulse widths between the pintle and disk type
injectors can be attributed to weight differences. The Lucas disk
only weights .4g while the pintles used by Bosh/Nippon-Denso weight
4g ten times heavier! The disk's lighter weight offers reduced inertial
loading allowing it to overcome hydro-static load faster and return
to its seat quicker. This decreases response times of the pulse
widths and also provides a more constant cycle to cycle flow.
Most pintel injectors tend to fail at around 86% duty cycle while
the disk type injectors can usually go to 90% duty cycle. This means
that the injectors will increase their flow rates until they reach
their highest duty cycle (listed above) and then go semi-static
or half-open just before going full static. At semi-static the injectors
are only delivering a 50% duty cycle flow rate and at static they
lock closed. This usually occurs when you are running WOT, high
RPM, and or max boost when you need 100% fuel delivery and your
only getting 50%. This situation creates a lean condition that will
have you shopping for a new engine fast. If you plan on running
higher fuel pressures be warned that at higher fuel pressures this
situation seems to be amplified a bit more. When choosing an injector
a larger than necessary injector running at a 70% duty cycle will
provide more controllable performance than one being pushed to 90%+.
Remember, when choosing an injector a larger than necessary injector
running at a 70% duty cycle will provide more controllable performance
than a smaller one being pushed to beyond 90%.
Atomization
When you consider that at 6000 RPM the intake valves are opening
50 times a second leaving only about .010 seconds to provide all
the necessary fuel. With such a brief intake valve open time you
may feel that having a fuel injector that delivers a wide highly
atomized pattern into the intake would be ideal to ensure a homogenous
mixture but this is not necessarily the case. At low RPMs highly
atomized fuel has enough time to pass by the intake valve and create
a homogenous mixture but as the RPMs increase problems start to
develop. In an engine running at high RPMs there is limited time
for the fuel to reach the combustion chamber. This is compounded
by the fact that often there is residual exhaust pressure present
when the intake valve is opened. The residual exhaust pressure tends
to blow the lighter drops of atomized fuel back into the intake,
which tends to adhere and condense to the intake walls. This presents
a few problems. Fuel "puddling" in the intake increases
drag thereby reducing airflow, large quantities of highly atomized
fuel can displace air in the port, and if the "puddled"
fuel does reach the combustion chamber it will cause air/fuel ratio
variances between cylinders.
Remember that by choosing the proper size of the injector based
on flow rate and duty cycle you will be able to avoid any injector
pit falls. This will leave you with plenty of time to worry about
other things such as, "how to increase the amount of fuel being
delivered to the injectors?"
|
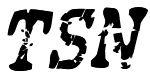
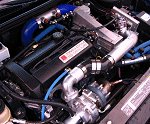

The turbosaturns.net
forum has become one of the best resources for Saturn performance
on the net. Our members are constantly pushing their cars to new
performance levels. So, log in, share your ideas, and help push
your car’s performance to the next level.
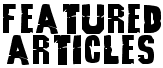
Archived Articles
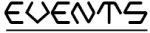
August 2005 TSN will be holding its first ever meet
in Chardon, Ohio. Some of the fastest Saturns in the country will
be attending. Activities will include drag racing, dyno, tech session,
and BBQ. Look for the latest information in the forums.

Different
Racing
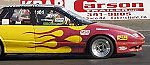
Jeff and his team Different Racing have big plans
on breaking into some really low quarter mile times this year. Last
year he posted a 12.40 on a pretty healthy nitrous shot. This year
he has a new turbo setup and some serious determination. Visit his
website for the latest news and information. I expect we'll be seeing
some low 12's from him by the end of the year.
|